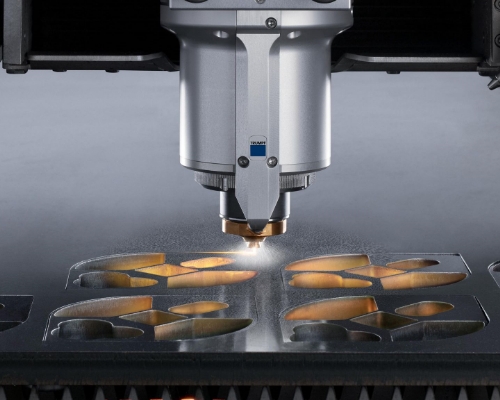
We have the most advanced (2500W)precision CNC cutting equipment and precision CNC bending equipment, it can save customer's early input of stamping die and shorten customer sample time. so that it can get to market faster.
We can process all kinds of sophisticated parts include welding and surface treatment. The maximum thickness of our laser cutting sheet is 20mm, aluminum sheet is 12mm, stainless steel sheet is 15mm, copper sheet is 8mm. We have been providing customers with the fastest sample processing. Our complex sample can be finished and shipped in 1-2 working days.
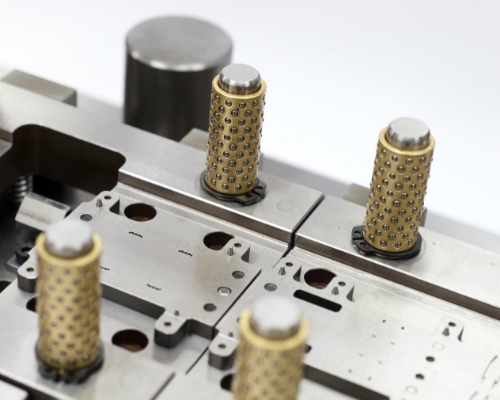
Our stamping die staff have nearly 20 years of manufacturing experience for precision stamping, precision stretching, fine blanking, forging and pressing. Our company's corporate culture: Always focused on sustained growth driven by technology as our mission. and we have all kinds of mold manufacturing equipment: Fast wire, low-speed wire, electric spark, CNC turning, precision grinder to guarantee mold dimensional accuracy. Every part we process need to be checked by a precision inspection equipment: CMM, YVM.
We use advanced mold design software:UG, CAD, Fro/E, 3D Max, solidwork etc. Our single die’s life time:1-2 million times. Our progressive die’s life time:5-10 million times. The brand of the part which our mold use is Japan Mismi and Punch and other first-class brands.
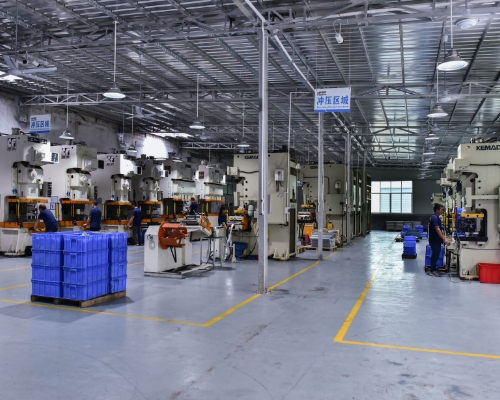
We have 20 sets of stamping equipment(80-200 tons)their brands are from China and Taiwan, all of them are pneumatic equipment. The Maximum product size we can process:1200mmX1000MM. stamping thickness is 0.8mm, Machining accuracy is 0.02mm. Our equipment is regularly maintained every day and every month(include reserve parts inventory) Our core competency is provide customers with flexible precision manufacturing:precision stretching, precision stamping, successive stamping. The successive stamping parts we produce are over 10 million pcs. They are used on European premium car brand...In addition we have Advanced control system: APQP, FMEA, SPC, MSA, PPAP.
The meterial we use :SPCC, SECC, galvanized plate, SUS301, 316, 303 AL5052, 6063 etc....

We have 10 sets of precision injection mold equipment. process size is 300mm X 300mm. The equipment brands are from Haitian(China)and Toshiba(Japan). Our current product are injection molding, metal encapsulating. The raw material we use are overseas brands designated by customers. The raw matrial we use are Compliance with ROSH and PEACH requirements. Our raw materials are sent to the company every 3 months for testing, so that it ensure all material meets customer standards.

We process different kinds of sophisticated parts come from aviation, optics, automobile and medical equipment field, The machining accuracy of our turning machine is 0.01mm-0.02mm. Our precision machining equipment brands are from Germany and Japan: MAZAK, KOMATSU, Brother, Toshiba, Emada etc. Our process material:aluminum alloy, copper alloy, magnesium alloy, stainless steel, titanium alloy. Our Maximum process size is 800mm X 800mm. Our manufacturing capability has been recognized by high-tech customers from all industries. Every part we process need to be checked by a precision inspection equipment to guaranteed quality.
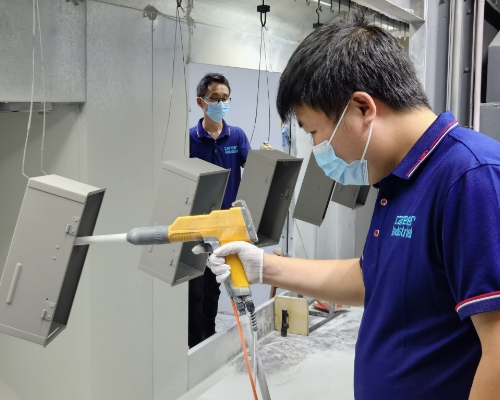
98% of our products are relate to different kinds of complicated surface treatment. Electroplate, electrolytic oxidation, hard anodizing, sand blasting, shot blasting, polishing, passivation, drawbenching, powder-coating, painting, UV, IML, IMD, color electrophoresis, corrosion, teflon, rubber paint. Appearance is a core competency for us, we have about 20 surface treatment engineer. They are proficient in different kinds of technical requirements and standards, For outdoor and indoor requirements, we perform 500-1000-2000 hour salt spray tests include corrosion resistance and other performance verification.
We provide our customers with the highest standards quality certificate:ISO9001, ITAF16949, ISO13485, AS9100, Nadcap, We have been recognized by the top 500companies:Flextronics, Jabil, Danaher, GE, ABB, Siemens, Logitech, LG, Samsung, Sony, Huawei, DJI, ZTE, BYD, Mindray etc....
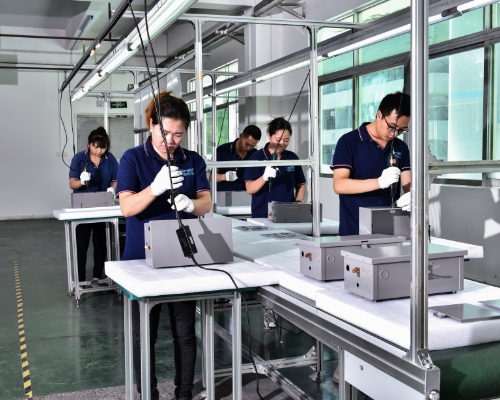
Our assembled products include metal stamping, injection molding, CNC machining precision complex components. The appearance requirements of these parts are very high, electronic PCB and electric motor use the brand specified by customers. We are only responsible for assembling and testing the technical standards.
Our staff are very familiar with the process and have over 5 years working experience. They are trained weekly by professional quality engineers so they are proficient in the product appearance and structure performance requirements. Our job standards for technicians and operators are:Perform and verify data according to SOP standards strictly.